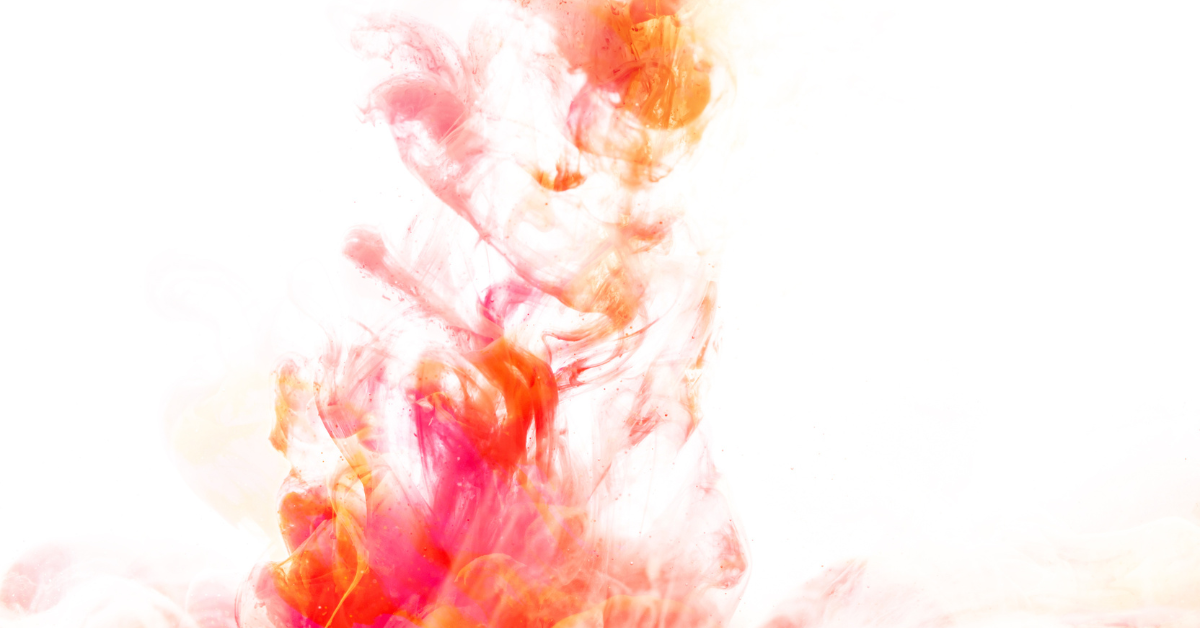
Dispersing Agents: The Role of Sophorolipid Biosurfactants in Greening Particle Dispersion
What Are Dispersants?
Dispersants are substances or chemicals that are used to improve the dispersion or uniform distribution of particles in a medium, typically a liquid. The primary goal of dispersants is to prevent agglomeration or clumping of particles, enabling them to remain stably dispersed throughout the medium. Dispersants find applications in various industries, including paints, inks, coatings, textile dyeing and more.
dispersant
dis·per·sant
noun
: a dispersing agent
especially : a substance for promoting the formation and stabilization of a dispersion of one substance in another
What Are The Key Functions Of Dispersing Agents?
Dispersing agents, also known as dispersants or dispersing aids, serve several essential functions in various industries where the dispersion of particles in a liquid medium is crucial. Here are the key functions of dispersing agents:
- Particle Dispersion: The primary function of a dispersing agent is to promote the even distribution of solid particles within a liquid. This prevents the particles from agglomerating or settling, ensuring a stable and uniform dispersion.
- Prevention of Agglomeration: Dispersing agents disrupt the attractive forces between particles, preventing them from clumping together or forming aggregates. This is particularly important in industries where the formation of agglomerates could hinder processes or product performance.
- Reduction of Surface Tension: Dispersing agents often reduce the surface tension of the liquid medium. By lowering surface tension, they improve wetting and spreading, enabling better contact between the liquid and solid particles.
- Improved Stability: Dispersing agents contribute to the stability of suspensions or emulsions by preventing phase separation. This stability is crucial in applications such as paints, inks and pharmaceutical formulations.
- Enhanced Reactivity: In industries where chemical reactions occur in a liquid phase, dispersing agents can enhance reactivity by ensuring a more uniform distribution of reactants. This is common in areas like chemical synthesis and polymerization processes.
- Facilitation of Mixing: Dispersing agents aid in the efficient mixing of different components within a liquid. This is essential in industries such as cosmetics, where consistent mixing of ingredients is necessary for product quality.
- Improved Product Performance: In applications like CASE and I&I Cleaning, dispersing agents contribute to the overall performance of the product by ensuring that the active ingredients are uniformly distributed and effectively delivered.
- Prevention of Sedimentation: Dispersing agents play a crucial role in preventing the sedimentation of solid particles in suspensions. This is especially important in industries such as wastewater treatment, where maintaining particle suspension is vital for effective treatment processes.
- Facilitation of Dyeing Processes: In the textile industry, dispersing agents are used to aid in the dispersion of dyes, ensuring even color distribution during dyeing processes.
- Environmental Remediation: Dispersing agents can be employed in environmental cleanup efforts to enhance the dispersion of contaminants in soil or water, facilitating their removal or degradation.
Overall, dispersing agents contribute to process efficiency, product quality and environmental sustainability in a wide range of industries. Their multifunctional nature makes them indispensable in applications where particle dispersion is a critical factor.
Classifying Dispersing Agents
When it comes to dispersants, they can be broadly categorized into two types based on their chemical composition: inorganic dispersants and organic dispersants.
Inorganic Dispersants
Inorganic dispersants represent a class of compounds devoid of carbon-hydrogen (C-H) bonds within their molecular framework. This category often includes metal-containing compounds or salts, such as sodium, potassium or ammonium compounds.
Notable examples encompass sodium polyphosphate, sodium hexametaphosphate and various metal hydroxides. In applications like ceramics, inorganic dispersants play a vital role by assisting in the dispersion of ceramic particles within liquid media during processing. Their inherent characteristics make them suitable for specific industrial processes where inorganic chemistry plays a crucial role.
Organic Dispersants
On the other hand, organic dispersants embrace compounds characterized by the presence of carbon-hydrogen (C-H) bonds in their molecular structure. This diverse category encompasses a wide range of substances, including surfactants and polymeric dispersants.
Examples of organic dispersants span various surfactant classes, such as nonionic, anionic, cationic or amphoteric surfactants. Additionally, polymeric dispersants, based on polymers featuring functional groups like carboxylates, sulfonates or amines, are integral members of this group.
Organic dispersants find extensive applications across diverse industries, including paints, inks, coatings, environmental remediation and agrochemicals. Their versatility stems from their ability to stabilize dispersions, prevent particle agglomeration and contribute to the overall efficacy of numerous formulations in complex processes.
The choice between inorganic and organic dispersants depends on factors such as the nature of the particles being dispersed, the properties of the liquid medium, and the specific requirements of the application. Both types of dispersants have their unique advantages and are selected based on the desired outcomes in the formulation process.
Examples Of Organic Dispersing Agents
Organic dispersants encompass a diverse range of compounds that share the characteristic of containing carbon-hydrogen (C-H) bonds in their molecular structure. These dispersants are crucial in various industries for stabilizing dispersions, preventing particle agglomeration and facilitating processes such as pigment dispersion in paints and inks. The different types of organic dispersants include:
Surfactants
Surfactants, or surface-active agents, are a broad category of organic dispersants that possess both hydrophilic (water-attracting) and hydrophobic (water-repelling) parts. Surfactants function as dispersing agents by lowering the surface tension between particles and the liquid medium, allowing for effective dispersion. They are classified into different types based on the nature of the hydrophilic or hydrophobic groups:
- Anionic Surfactants: Contain negatively charged hydrophilic groups, commonly found in soaps and detergents.
- Cationic Surfactants: Feature positively charged hydrophilic groups, often used in fabric softeners and antimicrobial agents.
- Nonionic Surfactants: Lack charged groups and are versatile, used in a wide range of applications, including emulsifiers and stabilizers.
- Amphoteric Surfactants: Contain both positively and negatively charged groups, providing versatility in different formulations.
Polymeric Dispersants
Polymeric dispersants are organic dispersants that consist of long-chain polymers with functional groups. These polymers contribute steric hindrance, preventing particles from coming into close contact. Common types of polymeric dispersants include:
- Polyacrylic Acid Dispersants: Feature carboxylic acid functional groups and are commonly used in water-based formulations like paints and coatings.
- Polyphosphonate Dispersants: Contain phosphonate functional groups and are effective in dispersing particles in aqueous systems.
- Polymeric Surfactants: Combine the properties of polymers and surfactants, providing both steric and surface activity.
A Closer Look At How Surfactants Act As Dispersing Agents
Surfactants act as dispersants by altering the surface tension of a liquid, which in turn affects the interactions between particles in that liquid. Here’s a simplified explanation of how surfactants function as dispersants:
Surface Tension Reduction
Surfactants, short for surface-active agents, have a unique molecular structure with hydrophilic (water-attracting) and hydrophobic (water-repelling) regions. When added to a liquid, surfactants migrate to the liquid-air or liquid-solid interface.
Hydrophobic Interaction
The hydrophobic tails of the surfactant molecules are attracted to particles or substances that are insoluble or less soluble in water. These hydrophobic interactions disrupt the cohesive forces between the particles, reducing their tendency to clump together.
Micelle Formation
Surfactants can form structures called micelles in the liquid. In a micelle, the hydrophobic tails cluster together to form the core, while the hydrophilic heads face outward, interacting with the surrounding liquid. This encapsulation of hydrophobic particles or substances within the micelle helps keep them dispersed in the liquid.
Stabilization of Dispersed Particles
The surfactant molecules create a stable environment for the dispersed particles by preventing them from coming back together. This stability is crucial in various applications, such as preventing sedimentation in wastewater treatment or maintaining the dispersion of oil droplets in oil spill response.
Improved Mixing and Efficiency
By reducing surface tension and promoting even distribution, surfactants enhance the mixing of substances in the liquid. This is particularly beneficial in industrial processes, where uniform dispersion can improve the efficiency of reactions or treatments. Surfactants used as dispersants are indispensable in various industries where their efficacy determines the efficiency of crucial processes.
Case Study: Pigment Dispersion In Fabric Dyeing Formulations
To achieve uniform and trouble-free dyeing, it is imperative that the dye be present in the dye bath in a finely dispersed and stable form. To address this, a specialized chemical known as a dispersing agent is employed. These agents must effectively operate under dyeing conditions, remain stable in the presence of hard water, high temperature and other dyeing assistants, ensuring consistent and reliable dispersion.
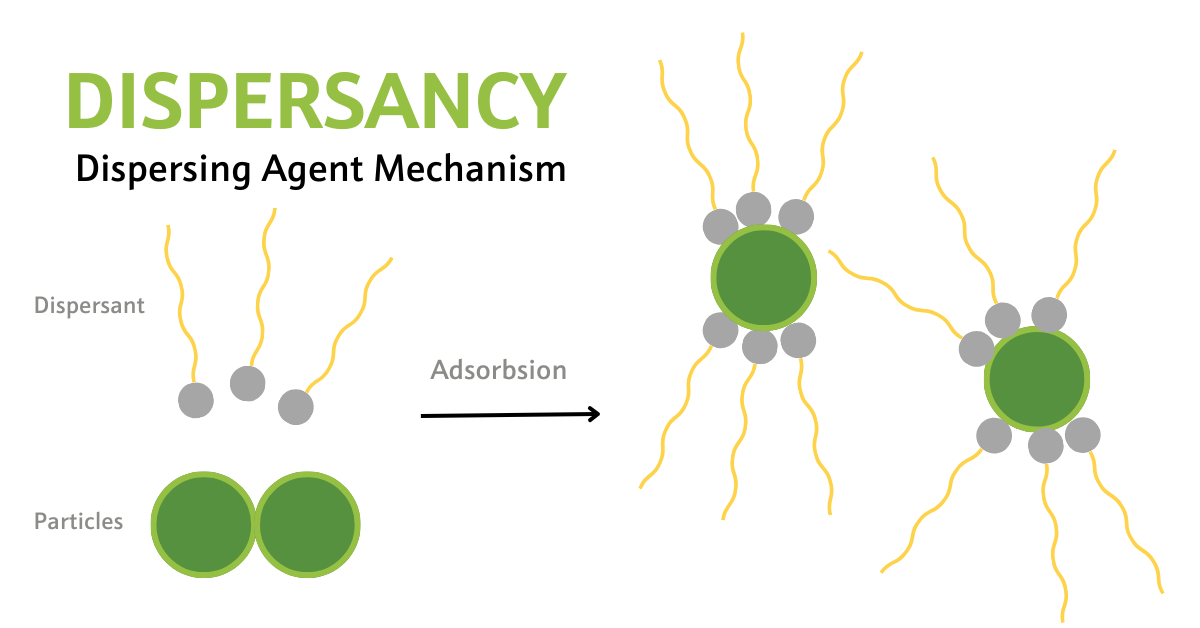
Fig. 1: Mechanism of Dispersion in an Aqueous Environment
Disperse dyes, inherently insoluble in water, form aqueous dispersions when introduced into water. Initially, these dye molecules exist as large particles, requiring size reduction through grinding. However, due to their water insolubility, direct use in the dye bath can result in uneven dyeing.
In the context of aqueous pigment dispersions, such as those found in colorants like fabric dyes, surfactants play a dual role. They must facilitate the milling process of pigments, ensuring effective breakdown and dispersion, while also providing essential stabilization for the dispersed pigment. Simultaneously, these surfactants must guarantee compatibility during the letdown process and contribute to optimal application performance.
Dispersing agents exhibit effectiveness in dyeing conditions and demonstrate stability in the presence of challenges such as hard water, high temperature and other dye assistants. Their role is essential in maintaining the dispersion of dye molecules within the dye bath.
Simplifying Dispersion: A Three-Step Process
The process of pigment dispersion typically involves a three-step approach to ensure uniform distribution of pigment particles in the formulation. These steps are essential for achieving consistent color, stability and performance in the final products. The three-step process includes:
- Pre-Wetting or Wetting:
The first step is pre-wetting, where the pigment particles are brought into contact with the liquid medium, such as water or a solvent. Pre-wetting aims to wet the surfaces of the pigment particles, breaking down initial agglomerates and ensuring that each particle is surrounded by the liquid. This step helps prepare the pigments for the subsequent dispersion process.
- Dispersion:
The dispersion step involves mechanical agitation to break down pigment agglomerates and achieve a uniform distribution of individual particles throughout the liquid medium. High-speed dispersers, ball mills or bead mills are commonly used for this purpose. Mechanical forces applied during dispersion break apart pigment clusters, reducing particle size and promoting even dispersion. Dispersing agents or surfactants may also be added at this stage to enhance wetting, reduce inter-particle forces and prevent re-agglomeration.
- Stabilization:
Stabilization is the final step to ensure the long-term stability of the pigment dispersion. This involves the addition of dispersing agents or stabilizers that provide a repulsive force between pigment particles, preventing them from re-agglomerating and settling over time. Stabilization is crucial for maintaining the dispersion’s integrity during storage, transportation and application. The choice of dispersing agents and their concentration is carefully considered to achieve the desired stability.
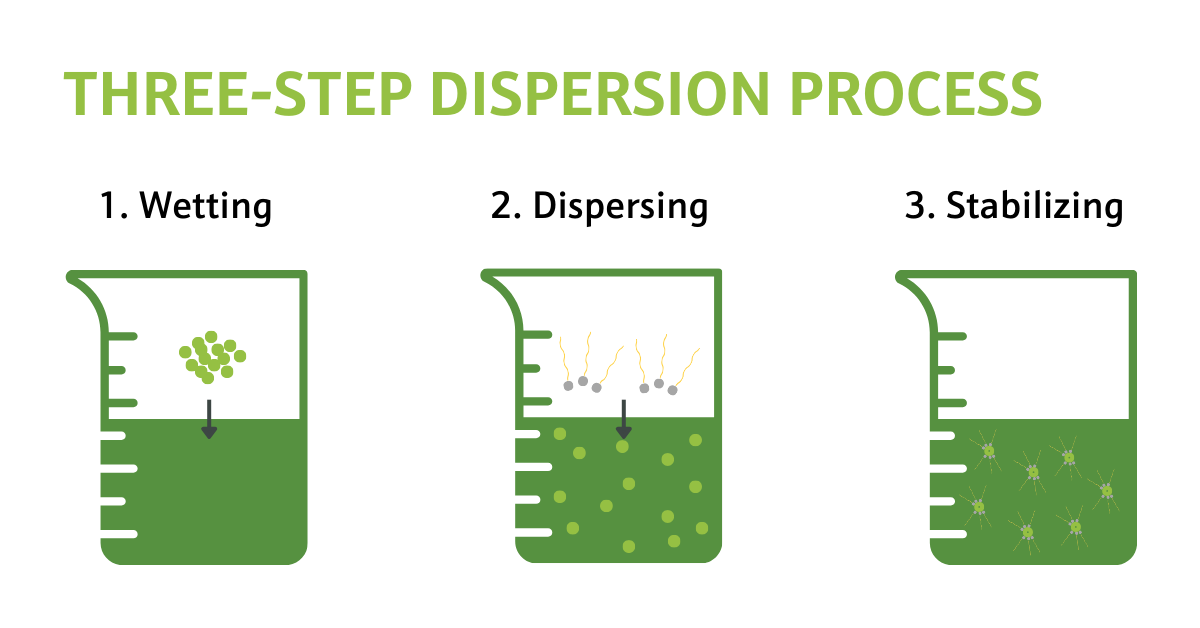
Fig. 2: Simplified Three-Step Dispersion Process in an Aqueous Environment
Throughout this three-step process, factors such as pH adjustments, temperature control and the use of milling equipment may be employed to optimize dispersion. The goal is to produce a stable and well-dispersed pigment formulation that can be easily incorporated into the final dye, paint or ink product. Proper pigment dispersion is critical for achieving consistent color development, color intensity and overall performance in the end-use applications.
Thinking Beyond Traditional Chemical Dispersing Agents
While traditional chemical surfactants have proven effective as dispersing agents in various applications, they come with certain concerns and drawbacks that have led to a growing interest in alternative solutions. Some of the key concerns associated with traditional chemical surfactants include:
- Environmental Impact: Many traditional surfactants are derived from petrochemical sources, contributing to environmental concerns. The production and use of these surfactants can lead to the release of non-biodegradable compounds and contribute to pollution.
- Biodegradability: Some traditional surfactants may have low biodegradability, meaning that they persist in the environment for extended periods, potentially causing long-term ecological impacts.
- Toxicity: Certain chemical surfactants may exhibit varying levels of toxicity, raising concerns about their impact on aquatic life and other organisms. This is particularly significant in formulations that are released into water systems.
- Health and Safety: The use of traditional surfactants may pose risks to human health, especially in occupational settings where exposure levels are higher. This includes concerns related to skin irritation, respiratory issues and other potential health hazards.
- Regulatory Compliance: Increasing regulatory scrutiny and a growing emphasis on sustainability have led to stricter environmental regulations. Formulations containing traditional surfactants may face challenges in meeting evolving regulatory standards.
Addressing these concerns has led to the exploration of alternative dispersing agents, such as bio-based surfactants. Researchers and industries are actively pursuing innovative solutions that prioritize environmental sustainability and biodegradability alongside improved performance and profitability, aiming to overcome the limitations associated with traditional chemical surfactants.
In this regard, 100% bio-based surfactants, like sophorolipid biosurfactants from Locus Ingredients, emerge as a sustainable alternative, offering a promising solution to the environmental challenges posed by traditional surfactants.
Biosurfactants As Eco-Friendly Dispersing Agents
Locus Ingredients’ line of Amphi® biosurfactants are produced through natural fermentation, not traditional chemical synthesis. The ingredients used in the fermentation process are responsibly sourced, natural sugars and oils. Further, the entire line is categorized as readily biodegradable, which means at least 60% biodegrades in the first eight days after being released into the environment.
Amphi biosurfactants are non-toxic, containing no 1,4-dioxane, ethylene oxide, formaldehyde or other Proposition 65 chemicals of concern. The line has earned the USDA Certified Biobased Product label for containing 100% biobased, renewable content, which is a stark differentiation from many other so-called “bio-based” ingredients, that are actually only partially bio-based.
Ready To Start Formulating?
Review the checklist below and reach out to our team if you have any questions. Our tech service department can help you every step of the way, from our ready-to-use formulation library, to application-specific customization and blending suggestions.
Formulation Checklist: How To Select The Right Dispersing Agent
Selecting the right dispersant for a particular formulation involves considering various factors to ensure optimal performance and stability. Here are some key questions to ask when choosing a dispersant:
Nature of Particles – What are the characteristics of the particles to be dispersed? Consider factors such as particle size, surface charge and composition.
Liquid Medium – What is the nature of the liquid medium (solvent or water)? Consider the compatibility of dispersant with the medium and the intended application.
Chemical Compatibility – Is the dispersant chemically compatible with other components in the formulation? Ensure that the dispersant does not react adversely with other ingredients.
pH Requirements – What is the pH of the formulation? Some dispersants may be more effective in specific pH ranges. Consider adjusting the pH if needed.
Temperature Sensitivity – What are the temperature conditions during processing and application? Ensure that the dispersant remains effective under the intended temperature range.
Application Type – What is the intended application of the formulation (e.g., paints, inks, coatings, pharmaceuticals)? Different applications may require dispersants with specific properties.
Stability Requirements – How stable does the dispersion need to be over time? Consider the shelf life and storage conditions, and choose a dispersant that provides adequate stability.
Toxicity and Environmental Impact – What are the toxicity and environmental considerations? Opt for dispersants that align with regulatory standards and environmental sustainability goals.
Surfactant Type – Does the formulation benefit more from anionic, cationic, nonionic or amphoteric surfactants? Consider the specific requirements of the system.
Polymeric Dispersants – Is the use of polymeric dispersants more suitable for the formulation? Evaluate whether the addition of long-chain polymers with specific functional groups would enhance stability.
Cost Considerations – What is the budget for the formulation? Consider the cost-effectiveness of different dispersant options while ensuring they meet performance requirements.
Regulatory Compliance – Does the dispersant comply with relevant regulatory standards and certifications? Ensure that the chosen dispersant aligns with industry regulations and safety standards.
Particle Size Distribution – What particle size distribution is desired in the final product? Choose a dispersant that can effectively control and optimize particle size.
Interaction with Other Additives – How does the dispersant interact with other additives in the formulation? Consider potential synergies or conflicts with other components.
Application Method – How will the formulation be applied (e.g., spraying, brushing, printing)? Consider the application method to ensure compatibility with the dispersant.
By addressing these questions, formulators can make informed decisions and choose dispersants that align with the specific requirements and goals of their formulations.
READ MORE: Coalescing Agents Transformed
Unleashing the Potential of Sophorolipid Biosurfactants
Coalescing agents, crucial in applications like paint formulation, play a pivotal role in enhancing film formation and coating properties. They facilitate the merging of small droplets in a liquid medium, ensuring a seamless and cohesive end result.